Compare
Clear
DrivesMatrixTM
Remote Monitoring and Troubleshooting
The future of industry is here
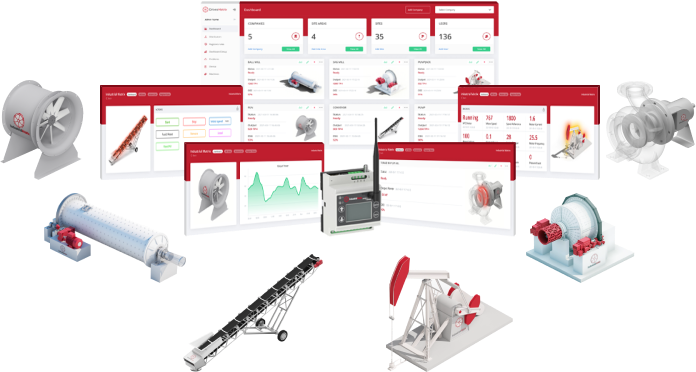
Connect any machine online
through
through
DrivesMatrix
- Better serve your customers through remote monitoring and troubleshooting
- Expand your product offering and create new sources of recurring revenue
- Build a strong competitive advantage through cutting edge, Industry 4.0 technology
How it works
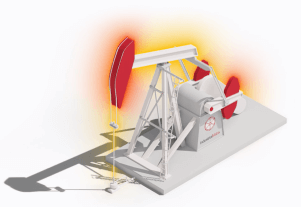
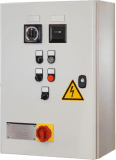
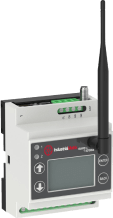
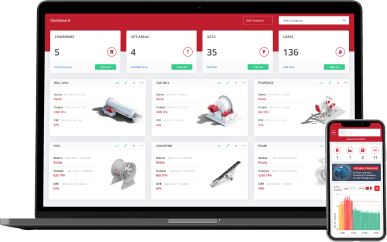
PLC / Drives
Contains all operational information of the asset
Controller
Edge Gateway sends equipment data to the cloud
Customized Dashboards
Pick from over 1000 parameters to monitor and visualize your operation live
Alerts
When an issue is detected, notifications are sent via text or email in real time
Remote Troubleshooting
Resolve issues remotely by updating machine’s parameters online. Reduce downtime and operational costs
Product Features
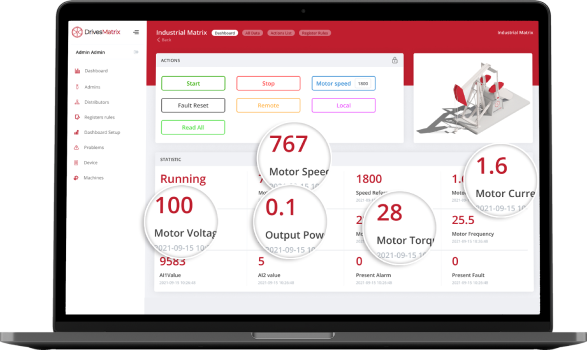
-
Easy to Deploy and Scale
Add a small edge gateway to a PLC or Drives and automatically put an entire machine online. Quickly deploy & scale to all your customers
-
Remote Monitoring
Track over 1000 operating parameters, including: speed, power, current and torque. Set rules to autonomously identify anomalies based on predefined values
-
Notifications
Setup thresholds, warnings and alerts levels. Get notified in real time, via text or email, when an issue is detected
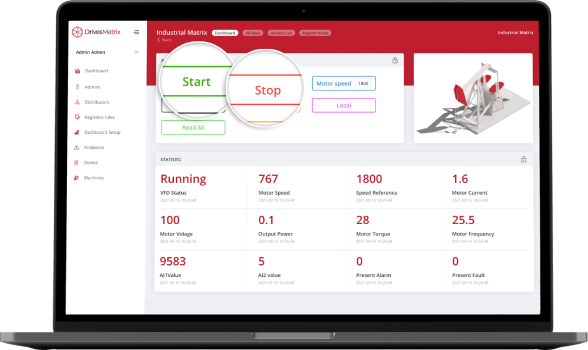
-
Remote Troubleshooting
Resolve issues remotely by updating machine’s parameters online. Reduce downtime and operational costs
-
Remote Control
Start, stop and change motor speed remotely. Reset faults to keep an asset running. Choose from +1000 parameters and create commands to build a customized control panel
-
Retrofit
Add DrivesMatrix to existing equipment in the field
Custom Dashboards based on customer’s needs
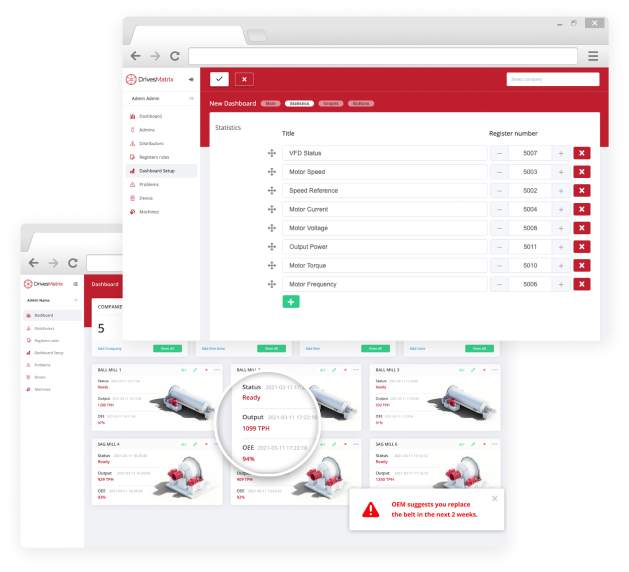
1
OEE, operating
characteristics
characteristics
System manages and measures output, showing overall equipment
efficiency (based on your production requirements)
2
Monitor equipment
anywhere, anytime
anywhere, anytime
Know how your machines are operating in the field in real time
3
Maintenance
suggestions
suggestions
Create maintenance suggestions based on performance and operations events that can be predefined in the system
4
Actionable
insights
insights
Create custom dashboards and show meaningful data based on your specific needs
Added Value - Predictive Maintenance
Enable customers to predict and prevent failures in real time, increase asset lifetime and strengthen the reliability of their operation
Add PDMMatrix as an offering within the DrivesMatrix platform
- Temperature and vibration
- Current Monitoring
- Ultrasound
- LubeMatrix
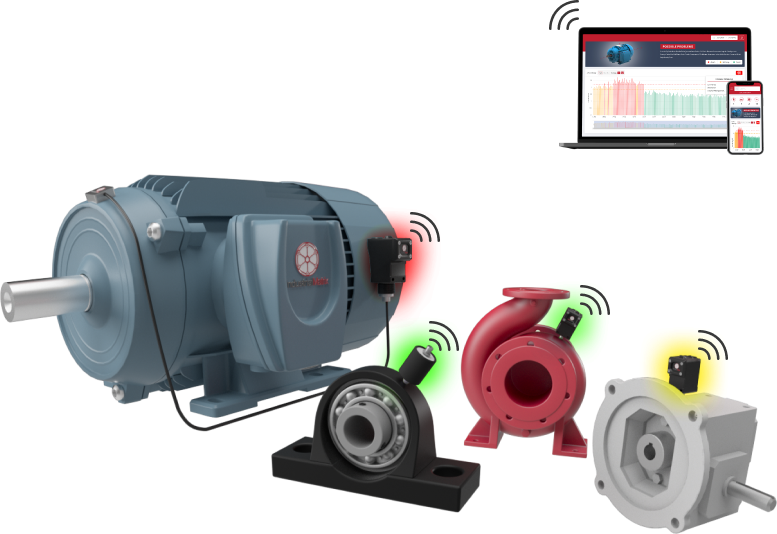
Business Case
SaaS
model
Generate an additional source of recurring revenue by offering a new
software service to your clients (interface can be designed with your branding,
powered by Industrial Matrix)
Data driven
planning
Insights into customer’s potential equipment failures ensure spare part
availability and added maintenance services
Gain new
business
Stay ahead of the competition by offering cutting edge, Industry 4.0 technology.
Minimal upstart investment required
Added
services
Create a remote monitoring service and keep track of client’s equipment for them
Increase customer satisfaction
Retrofit existing customer’s equipment and provide remote services with
DrivesMatrix
Warranties
Monitor machine operations, detect product misuse and mitigate false warranty claims
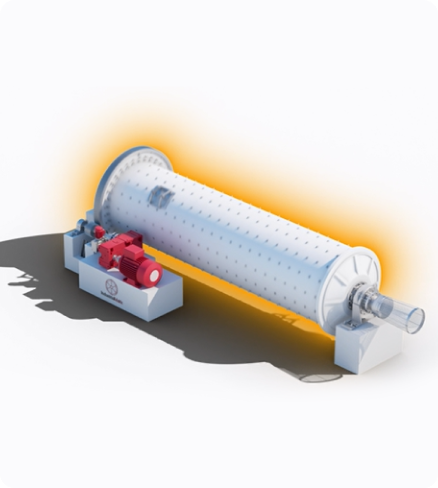
Schedule a meeting
Follow the link below to learn more about the system and schedule a meeting with one of our experts
Book now