Compare
Clear
Condition Based Lubrication
Revolutionizing how bearings are monitored and lubricated
Prevent lubrication-based failures, reduce downtime,
and ensure that bearing maintenance always gets done!
and ensure that bearing maintenance always gets done!
Condition based lubrication powered by real time data
Why Ultrasound? How it works
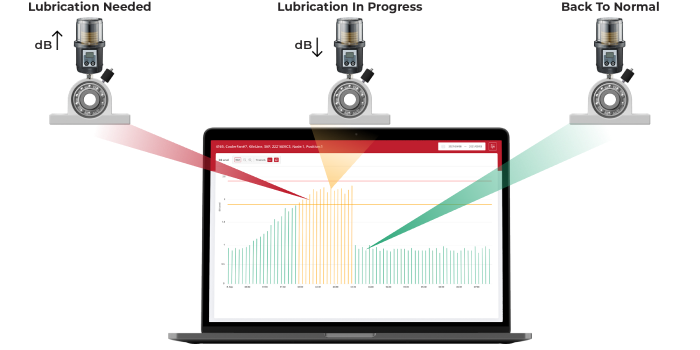
Early iteration of a bearing repairing itself!
Using ultrasound technology, lubrication is automatically performed based on real time data that asses the condition of the bearing.
Plug & play solution ensures that bearing maintenance always gets done.
Set It & Forget It!
Baseline
Baseline is set at normal operating conditions
Sensor
Ultrasound sensors monitor dB (friction) in real time and asses bearing health
Cloud
Lube Logic algorithm analyses data in real time and takes corrective action
Lubrication
Bearings are autonomously lubricated at the right time, with the exact amount needed
Solution Benefits
-
Convenience
Reduce manual workload and continuous in-person checkups. Solution ideal for remote, constricted and hard to reach areas.
-
Reduced downtime
Actively prevent lubrication-based failures to keep your plant running.
-
ROI
Increase the life of your bearings, reduce operational costs and optimize energy use.
-
Easy to scale
Monitor up to 100 bearings with a single controller within 10 KM line of sight range.
-
Bearing health
Detect other bearing issues with condition monitoring.
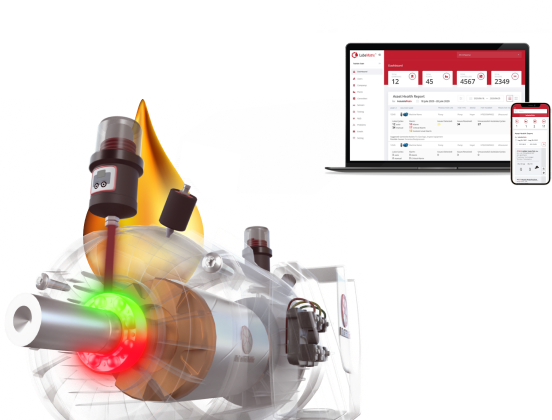
Product Offering
Single-Point Lubrication
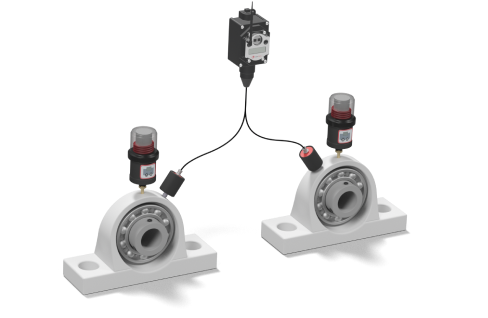
-
Notifications
System sends an alert when the lube reservoir needs to be replenished or when a bearing issue is detected
-
Install
Ultrasound sensors are affixed to the bearings (drill & tap or epoxy) and Autolubers are screwed into the grease fitting
-
Convenience
Autolubers have grease pouches for easy replenishment
Multi-Zone Lubrication
-
Precision Lubrication
System only greases the lube points that need to be lubricated
-
Flexibility
Solution enables user to autonomously lubricate multiple lube points, or the entire system, based on condition
-
Notifications
System sends an alert when the lube reservoir needs to be replenished or when a bearing issue is detected
LubeMatrixTM-
Software Benefits
Monitor bearing condition
wherever you are, 24/7
wherever you are, 24/7
Live dashboards
Trend issues and make split second decisions to keep your plant running
Lubrication
Automatically or manually lube your assets through the cloud
Notifications
Get notified when it is time to replenish the lube reservoir
Alerts
Via text or email, in real time, when a bearing issue is detected
Asset Health
Trend bearing condition
Revolution
Lube Logic will enable
your bearings to repair themselves powered by
real time data
your bearings to repair themselves powered by
real time data
Real Time Monitoring, Precision Lubrication
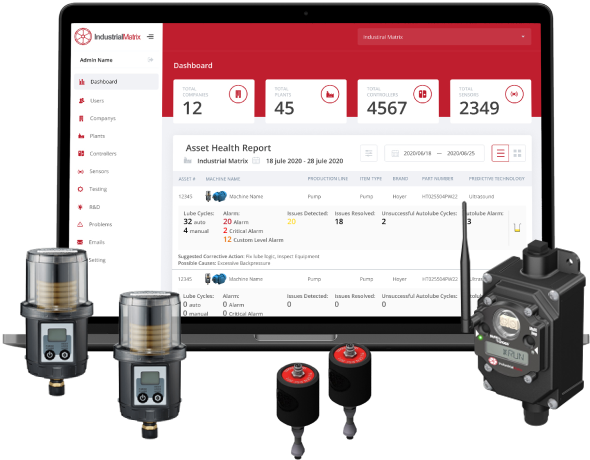
Intuitive, easy to use interface provides actionable insights
Schedule a meeting
Follow the link below to learn more about the system and schedule a meeting with one of our experts
Book now