Compare
Clear
Meat Processing
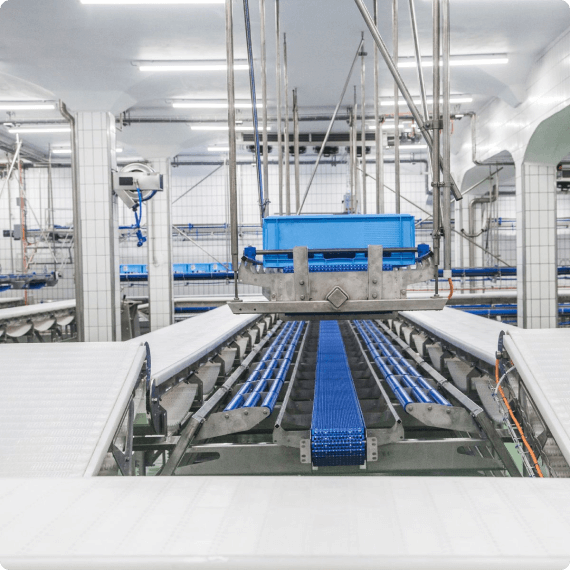
Challenges
Maintenance at a meat processing plant is challenged by the need to uphold stringent hygiene standards while ensuring uninterrupted operation of complex machinery like slaughter lines, grinders, and packaging equipment. Preventive maintenance scheduling is crucial to minimize downtime and avoid disruptions in production, which can lead to significant financial losses.
Applications
- Overhead Rail
- Saws
- Shackle Chain
- Cold Water Pump
- Dehair
- Chillers
- Singer
- Rinser
- Compressor
Case Study: Meat Processing
Program installed on Feb 11th 2024. After a week of production set thresholds and discussed the day over day trend of increasing accelerations on this motor. Comparing this to the similar application of the Final Chill Motor, not only were the amplitudes significantly different, but the Final Chill Motor was steady day to day.
Triggering our first warning on Mar 9th, we began planning the motor replacement. On Mar 30th, we replaced the motor and saw immediate improvement dropping the acceleration from 2 g’s down to 0.1 g’s. Labour cost is calculated at $25/hour for 300 employees. Estimated repair time would cost 4 production hours.
$25*300*4= $30,000
An additional 4 hours of production would be required to cover for the downtime.
($25*1.5)*300*4=$45,000
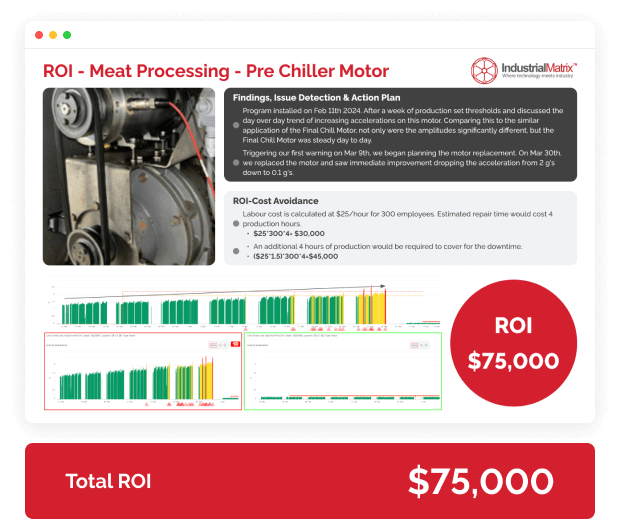
Schedule a meeting
Follow the link below to learn more about the system and schedule a meeting with one of our experts
Book now