Compare
Clear
Bottling
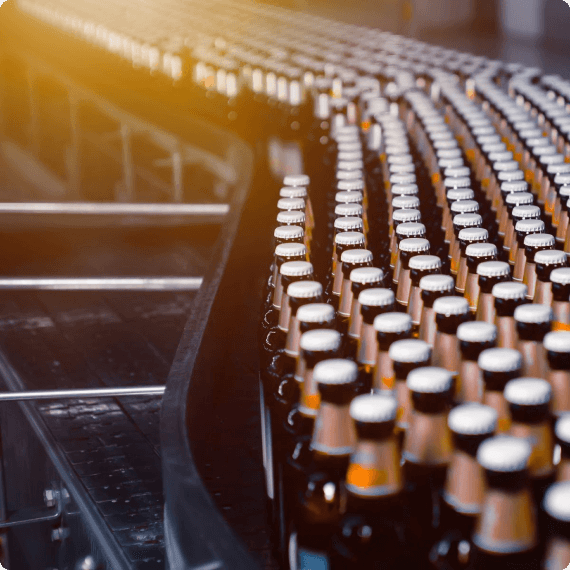
Challenges
Maintenance at bottling plants is a demanding task, driven by the need to keep high-speed production lines running smoothly while adhering to strict hygiene standards and ensuring compliance with safety regulations. Managing spare parts and conducting timely preventive maintenance are critical to minimizing downtime and maintaining operational efficiency. Skilled maintenance personnel play a key role in troubleshooting and repairing complex machinery, such as fillers and labelers, essential for the continuous and safe production of bottled products.
Applications
- Filler
- Bubble Chain
- Capper
- Compressor
- Syrup pump
- Conveyor
- Deaerator
- Blower
- Vacuum
Case Study: Bottling Plant
Program started September 2023 with continuous temperature/vibration monitoring on 2 filler lines.
Wireless sensors sample data every 5 minutes alerting on issues in real-time, weekly analysis is performed.
In early January the vibration started increasing, triggering alarms indicating an issue with the gearbox.
An inspection showed the gearbox was failing, replaced Jan 11th.
Replacement takes 6 hours with a spare on hand, up to 24 hours without a spare + Rush delivery.
Cost of a new gearbox is $12,000, asset was in operation for 10 months but is normally replaced every 12 months.
Production downtime for this line is estimated at 2,000 cases/hr @ $3/case = $6,000/hour.
The condition-based replacement resulted in no mechanical downtime.
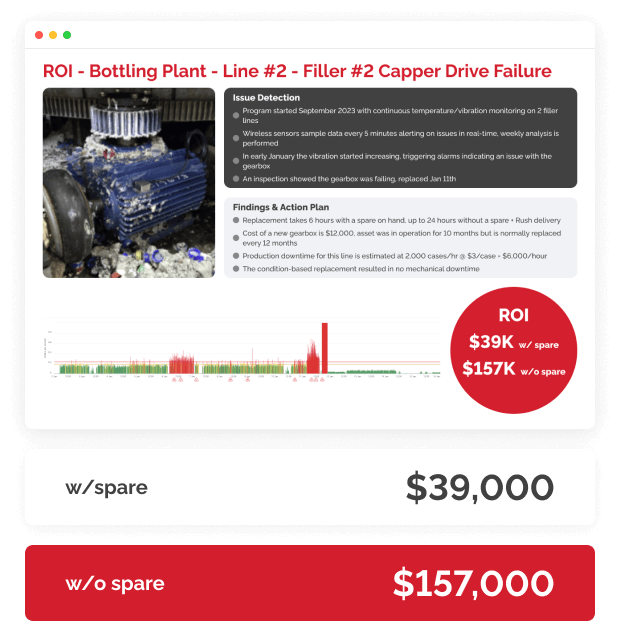
Schedule a meeting
Follow the link below to learn more about the system and schedule a meeting with one of our experts
Book now