Compare
Clear
Cement
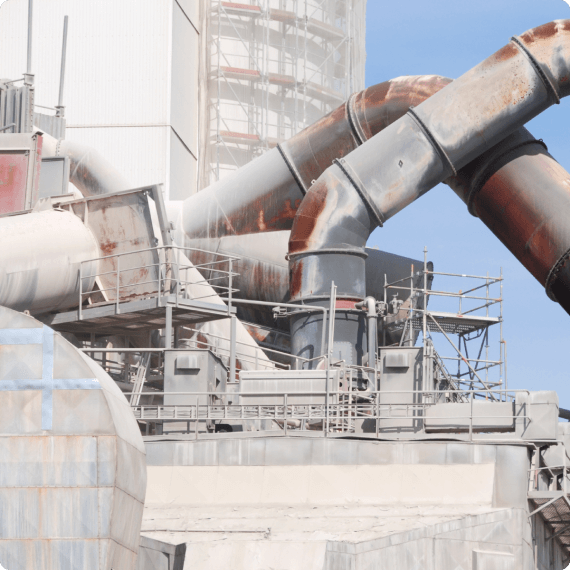
Applications
- Kilns
- Crushers
- Ball Mills
- Fans
- Separators
- Elevators
- Blowers
- Compressors
- Pumps
- Conveyors
Challenges
Maintaining a cement plant involves navigating a range of challenges due to its complex and demanding operational environment. Key concerns include ensuring high equipment reliability amidst harsh conditions, managing wear and tear on critical components like mills and kilns, optimizing energy efficiency to mitigate the industry's high energy consumption, and adhering to stringent environmental regulations.
Safety is paramount due to the hazardous nature of the equipment and materials used. Effective maintenance strategies, supported by skilled personnel and proactive management practices, are crucial to overcoming these challenges and maintaining efficient and reliable cement production operations.
Case Study: Cement Plant
Motor side sensor detected high acceleration in early May 2022, velocity increased later that month followed by temperature in early June 2022 - following the D-I-P-F curve.
Team determined the bearing failed; it was changed mid-June 2022 with 0 unplanned downtime.
The last failure was on April 8, 2019, losing the entire kiln for 27 hours as the shaft was damaged and had to be changed, the team worked through the night to repair.
2019 failure = $283,500 in lost production ($75/tonne x 27 hours @140 tonnes/hour).
2019 failure = $16,250 in components (new shaft & bearings) + $5,600 in overtime.
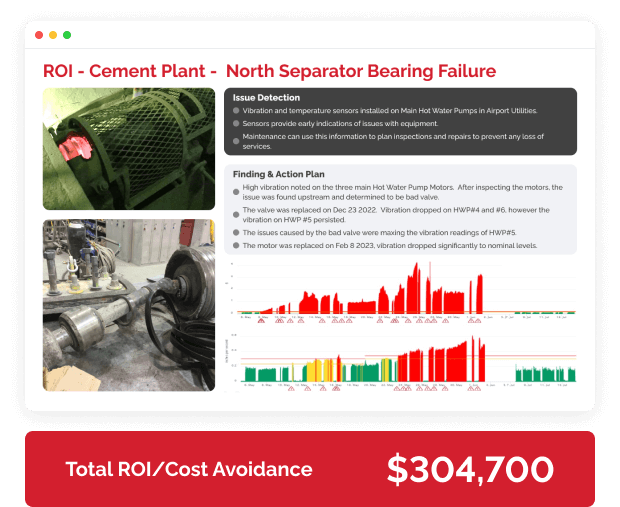
[5.0%]
Average overall reduction in downtime
$976,000
in documented cost avoidance
[39X+] ROI
on average subscription cost
Schedule a meeting
Follow the link below to learn more about the system and schedule a meeting with one of our experts
Book now